Metal Injection Moulding (MIM) is a metal parts manufacturing process that has become increasingly popular in a wide range of industries, from automotive to electronics and medical. It combines the versatility of injection molding technology with the ability to produce highly precise and complex metal parts. But how exactly does this process work?
Metal Injection Moulding (MIM) process
MIM process consists of several key stages, from the formulation of the raw material to the final sintering of the part. Let’s look at each of these stages in detail:
1. Mould design and manufacturing
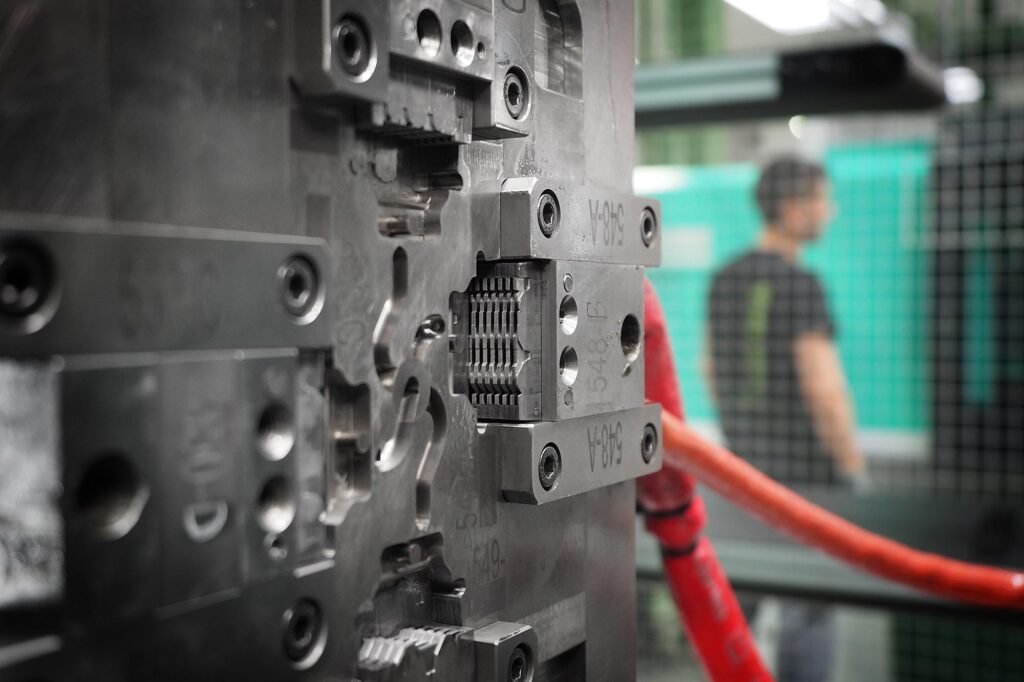
Mould prepared for MIM process
This first stage is one of the most critical in the whole process. The design itself involves a number of considerations, from part geometry, tolerances and manufacturability to mechanical properties and functionality. A multitude of factors must be taken into account to avoid downstream defects, and a correction factor must be applied in the design and manufacture of the part, which is defined by the material to be used. Attention to detail is fundamental to the success of the process and the quality of the final parts.
2.Powder and Binder Mix Formulation
The next step in the MIM process is the selection of the base material. This material is obtained by creating a mixture of fine metal powder and a thermoplastic binder. Metal powder can consist of a variety of metals, such as stainless steel, titanium, copper, nickel, among others. Binder is a material system with various components (polymers and other chemicals) that is used to bind the powder particles together and provide the necessary cohesion for the injection moulding process.
3. Mixing and Granulation
Once the powder and binder mixture has been formulated, it is mixed in a process similar to that used in the manufacture of plastics by extrusion. This mixture is granulated to create a uniform feed material that can be used in the injection molding process.
4. Injection Molding

Green parts after injection moulding
The next step involves feeding the powder/binder mixture (feedstock) into an injection moulding machine, similar to those used in the manufacture of plastic parts. At this stage, feedstock is progressively heated in the screw so that, when it comes out of the nozzle, the binder is in a liquid state. The material as a whole (binder + metal powder), converted into a soft mass, allows it to be formed into the desired shape in a mould.
5. Debinding
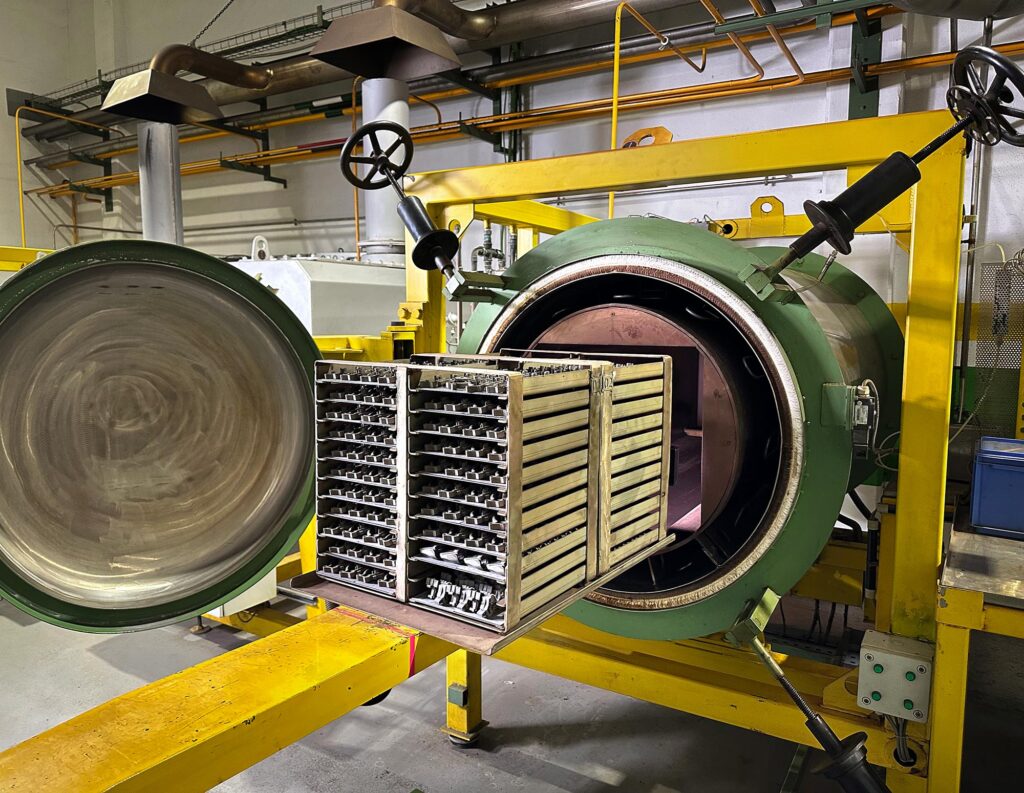
Catalytic Debinding Furnace
Once the moulded part has been removed from the mould, it goes through a process to remove the binder. This process can be done in 3 different ways: catalytic removal (chemical reaction between an acidic agent and the main component of the binder system), solvent removal or purely thermal removal. Each of these types of removal requires specific equipment and is a highly specialised process. The end result of debinding is a “preform” of minimally cohesive metal powder to preserve the geometry of the component. .
6. Sintering
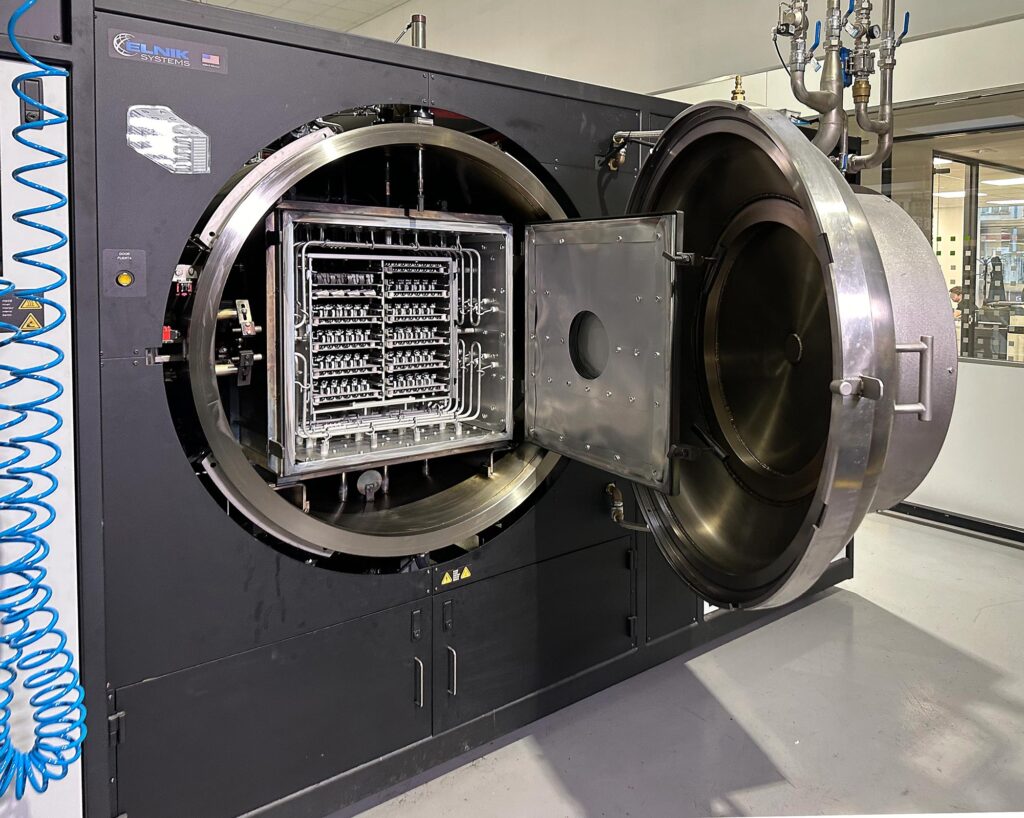
Sintering furnace in ALFA MIMtech
The resulting preform is then subjected to a sintering process, in which it is heated to a temperature high enough for the metal particles to join together, forming a solid, dense part. During this process, the part is reduced in size and densified.
7. Finishing
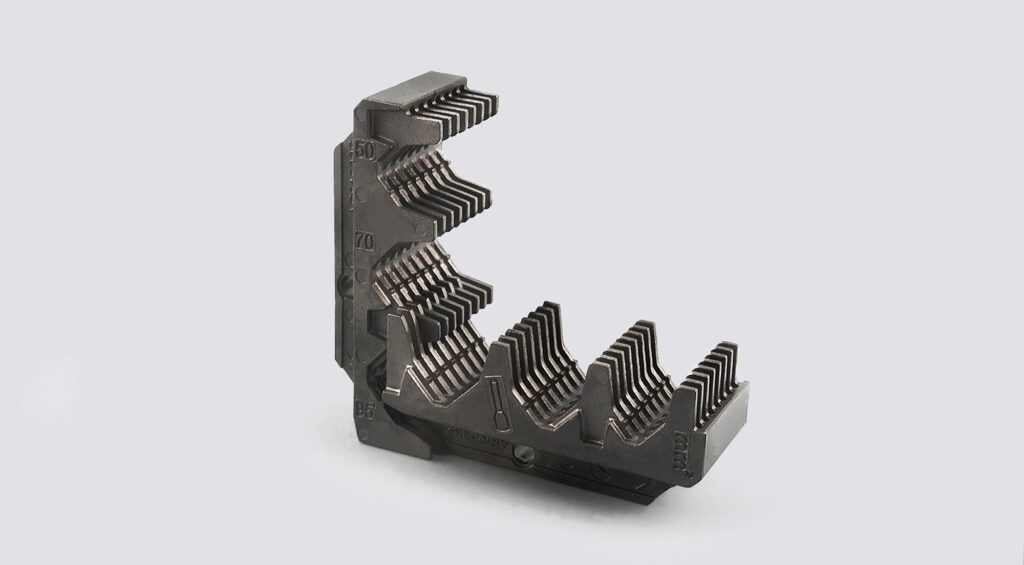
Sintered parts after Metal Injection Moulding process
Finally, the sintered part can undergo additional finishing operations and acquire the desired final mechanical properties, such as heat treatment, grinding, polishing, coating or other surface treatments according to the specific requirements of the application.
MIM Applications
MIM has become a widely used manufacturing technique in a variety of industries due to its numerous advantages. Some of the most common applications of MIM include:
- Precision components for the automotive industry, such as gears, valves and fuel systems
- Electronic components, such as connectors, contacts and device housings
- Medical tools and equipment, such as surgical instruments and implantation devices
- Precision components for the aerospace industry, such as fuel valves and control systems
- Wear parts and cutting tools for industrial applications.
Conclusions
Metal Injection Moulding is a versatile and efficient manufacturing technique that has revolutionized the way high-precision and complex metal parts are produced. With its many advantages, such as the ability to produce parts with intricate shapes and tight tolerances, MIM continues to be an attractive option for a variety of industries, from automotive to medical. However, it is also important to consider its challenges and limitations, and to carefully evaluate whether it is the right manufacturing method for a specific project.
Ultimately, the success of Metal Injection Molding lies in finding the right balance between cost, quality and production efficiency.