El desarrollo de la tecnología de Moldeo por Inyección de Metales (MIM) es una historia fascinante. Este proceso industrial ha revolucionado la fabricación de piezas metálicas complejas y de precisión. Veamos un recorrido detallado desde sus orígenes hasta su estado actual.
Antecedentes y orígenes de la tecnología MIM: la fusión de dos mundos
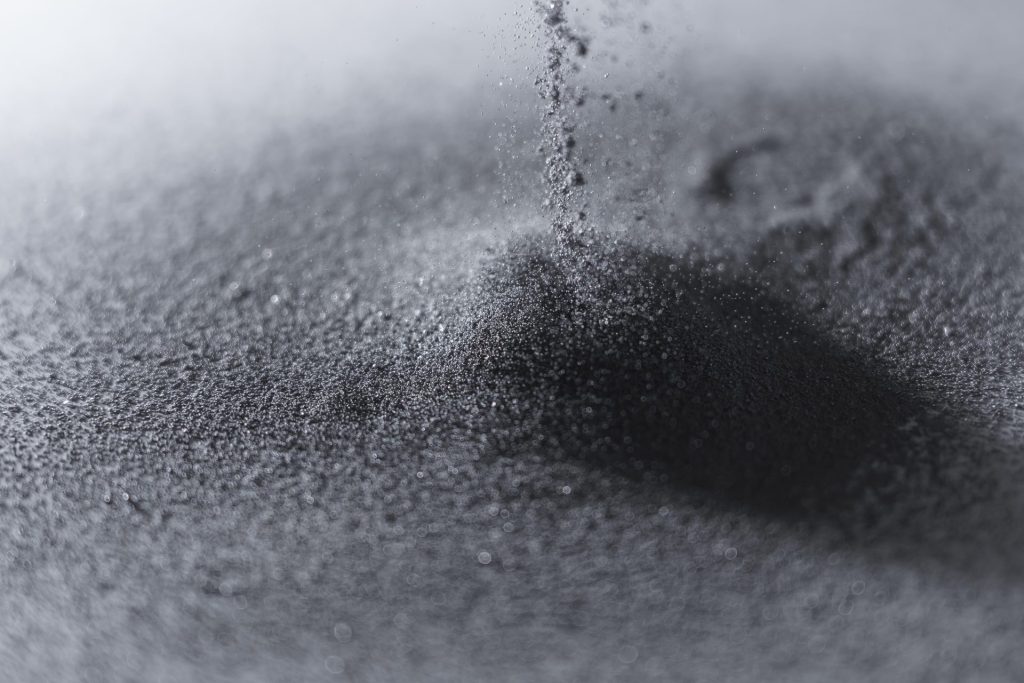
Polvo métálico base
La tecnología MIM no surgió de la nada, sino que fue el resultado de la convergencia de dos tecnologías de fabricación bien establecidas en el siglo XX: la Pulvimetalurgia (o Metalurgia de Polvos) y el Moldeo por Inyección de Plásticos.
- Pulvimetalurgia tradicional: Esta técnica, con raíces que se remontan a la antigüedad (los egipcios ya la usaban para fabricar objetos de hierro), consiste en compactar polvo metálico en un molde mediante alta presión para crear un «compacto en verde». Posteriormente, esta pieza se calienta en un horno a alta temperatura (sinterización) para que las partículas de metal se fusionen, obteniendo así una pieza sólida y densa. Sin embargo, la pulvimetalurgia tradicional estaba limitada en cuanto a la complejidad geométrica de las piezas que podía producir. Este proceso también se conoce como sinterizado tradicional o, en inglés, “press and sinter”.
- Moldeo por inyección de plásticos: Desarrollado en la primera mitad del siglo XX, este proceso permite la producción en masa de piezas de plástico con geometrías muy complejas. Consiste en inyectar un polímero fundido en un molde cerrado, donde se enfría y solidifica, adoptando la forma deseada.
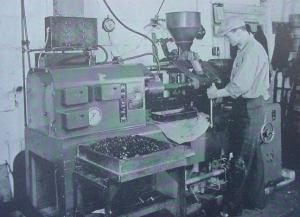
Máquina de inyección de plástico de los años 30
La idea seminal detrás del MIM fue: ¿Y si pudiéramos inyectar polvo metálico en un molde con la misma facilidad y libertad de diseño que el plástico?
Los pioneros y el nacimiento del concepto (Años 20 – 70)
Los primeros conceptos que se asemejan al MIM se remontan a la década de 1920, con intentos de moldear polvos cerámicos. Sin embargo, el verdadero impulso para el MIM como lo conocemos hoy comenzó mucho más tarde.
Los orígenes teóricos de lo que luego llevaría al desarrollo de la tecnología MIM datan de la década de 1950. En 1956, el científico soviético Petr Oskarovich Gribovsky publicó su estudio “Fundición en caliente de productos cerámicos”, donde estableció las bases conceptuales y teóricas para el MIM.
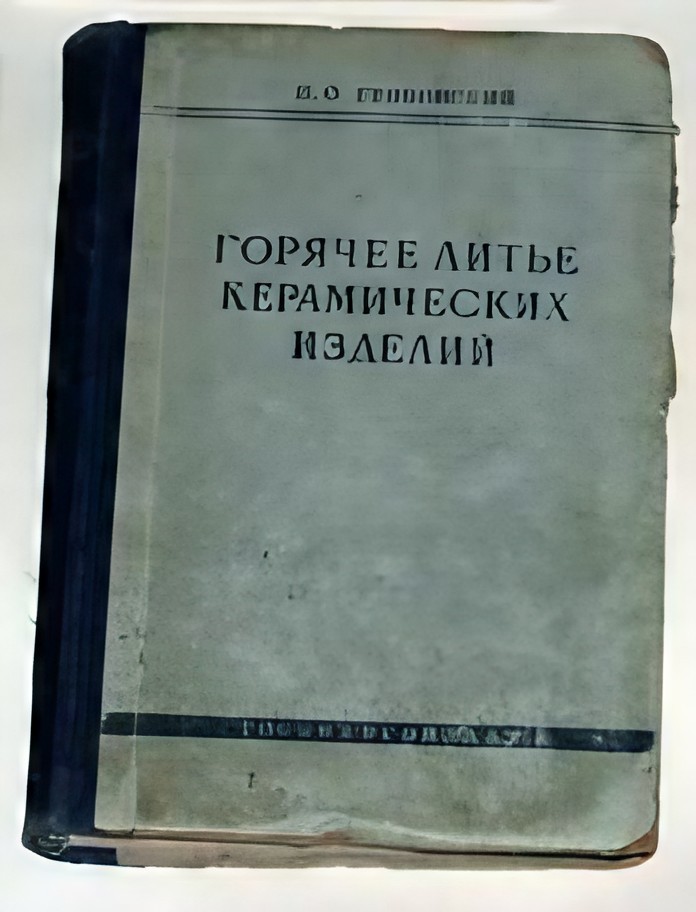
Edición de 1965 de «Fundición en caliente de productos cerámicos», de P. O. Gribovsky
Su trabajo describía una «tecnología de fundición en caliente proporciona la capacidad de fabricar productos a partir de cualquier material sólido, desde minerales naturales, óxidos puros, carburos, metales, etc., hasta materiales sintéticos compuestos multicomponentes y sus combinaciones”, aunque no se aplicó a un desarrollo industrial específico para obtener dichos productos.
Tenemos que adelantarnos 20 años para dar en Estados Unidos con el Dr. Raymond E. Wiech Jr., una figura clave en el mundo del MIM, considerado unánimemente como el «padre del MIM».
Mientras trabajaba en California, refinó los conceptos anteriores, adaptando el moldeo por inyección de plásticos a metales, y desarrolló y patentó el primer proceso MIM viable comercialmente.
El proceso MIM, una tecnología llena de desafíos
El Dr. Wiech y su equipo tuvieron la idea de mezclar finos polvos metálicos con un aglutinante termoplástico (un «binder»). Esta mezcla, denominada «feedstock», se comportaba como un plástico a altas temperaturas, permitiendo que fuera inyectada en un molde convencional de inyección de plásticos para formar una pieza «en verde».
Esta pieza era una réplica exacta de la cavidad del molde, pero estaba compuesta por partículas metálicas unidas por el aglutinante.
El desafío crucial era eliminar ese aglutinante sin distorsionar la pieza y luego sinterizarla hasta alcanzar su densidad final. Wiech desarrolló un proceso de dos etapas:
- Eliminación del aglutinante (Debinding): La pieza «en verde» se sometía a un proceso para eliminar la mayor parte del aglutinante. Inicialmente, esto se hacía mediante extracción con disolventes (“solvent debinding”) o calentamiento lento (“thermal debinding”).
- Sinterización: La pieza resultante, ahora muy porosa y frágil (conocida como pieza «en marrón»), se sinterizaba en un horno de atmósfera controlada a temperaturas cercanas al punto de fusión del metal. Durante este proceso, las partículas metálicas se fusionaban, la pieza se contraía de forma predecible y uniforme, y alcanzaba una alta densidad (típicamente superior al 95% de la teórica).
El trabajo de Raymond Wiech fue decisivo para que el MIM fuera adoptado industrialmente en los años 80. Sus desarrollos permitieron:
- Establecimiento de procesos reproducibles y escalables: Wiech logró estandarizar la formulación de mezclas de polvos metálicos y aglutinantes, así como los métodos de moldeo, desvinculación y sinterización, facilitando la producción en masa de piezas complejas con alta precisión y repetibilidad.
- Demostración de viabilidad comercial: Bajo su liderazgo en Parmatech, se fabricaron y comercializaron con éxito componentes reales para sectores exigentes como automoción, electrónica y médico, lo que validó la tecnología ante la industria y generó confianza en su adopción.
- Protección intelectual y difusión tecnológica: Las patentes de Wiech y la publicación de resultados técnicos ofrecieron un marco seguro y claro para que otras empresas pudieran invertir en la tecnología y desarrollarla, acelerando su expansión internacional.
- Reducción de costes y complejidad: Gracias a los avances de Wiech, el MIM se posicionó como una alternativa rentable frente al mecanizado y otros procesos de pulvimetalurgia, especialmente para piezas de geometría compleja y alto volumen de producción.
En 1980, la primera pieza MIM producida en masa, un rotor para un reloj, ganó un premio de la Metal Powder Industries Federation (MPIF), marcando un hito y dando a conocer la tecnología al mundo.
Evolución Tecnológica (Años 80 – Actualidad)
Desde los trabajos pioneros de Wiech, la tecnología MIM ha experimentado una evolución constante y significativa.
- Años 80: Expansión y nuevos actores:
- Tras el éxito inicial de la aplicación industrial del proceso diseñado por el Dr. Wiech, surgieron nuevas empresas que licenciaron la tecnología y comenzaron a desarrollar sus propios sistemas de aglutinantes y procesos.
- Se empezaron a procesar aleaciones más complejas, más allá de los aceros básicos, como aceros inoxidables y aleaciones de níquel.
- Años 90: Avances en aglutinantes y sinterización:
- Uno de los avances más importantes fue el desarrollo de sistemas de aglutinantes catalíticos. Este sistema, basado en polioximetileno (POM), permitía una eliminación del aglutinante mucho más rápida (en horas, en lugar de días) mediante el uso de ácido nítrico como catalizador. Esto redujo drásticamente los tiempos de ciclo y los costes, impulsando la adopción masiva del MIM en Europa y Asia.
- Se introdujeron sistemas de debinding por extracción con agua, que ofrecían una alternativa más ecológica a los disolventes.
- La mejora en los hornos de sinterización, con un control más preciso de la atmósfera y la temperatura, permitió procesar materiales reactivos como el titanio.
- Década de 2000: Miniaturización y nuevos materiales:
- Nace el Micro-MIM, enfocado en la producción de piezas de tamaño milimétrico o incluso submilimétrico con tolerancias muy estrictas. Esto abrió las puertas a aplicaciones en dispositivos médicos, microelectrónica y relojería de alta gama.
- Se amplió enormemente la cartera de materiales disponibles, incluyendo:
- Metales refractarios: Tungsteno, Molibdeno.
- Aleaciones de Titanio: Cruciales para aplicaciones médicas y aeroespaciales por su biocompatibilidad y relación resistencia-peso.
- Materiales Compuestos de Matriz Metálica (MMC): Por ejemplo, carburo de tungsteno-cobalto para herramientas de corte.
- Metales preciosos: Oro, platino.
- Década de 2010 y actualidad: Simulación, Automatización y Fabricación Aditiva:
- Simulación de procesos: El desarrollo de software avanzado permite simular el llenado del molde, la contracción durante la sinterización y predecir posibles defectos, optimizando el diseño de la pieza y del molde antes de fabricarlos.
- Automatización: La robótica y los sistemas de control de procesos en tiempo real han aumentado la repetibilidad y la eficiencia de la producción MIM.
- Conexión con la Fabricación Aditiva: Han surgido tecnologías híbridas que combinan la libertad de diseño de la impresión 3D con la capacidad de producción en masa del MIM. Por ejemplo, la tecnología Binder Jetting comparte muchos principios con el MIM (uso de polvo y aglutinante, seguido de debinding y sinterización) y se considera una tecnología complementaria así como otras tecnologías aditivas basadas en sinterizado (FFF, LMM, etc.).
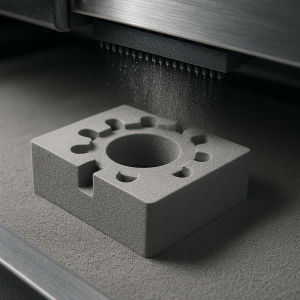
Binder jetting
Descubrimientos científico-tecnológicos clave
El avance del MIM se ha sustentado en descubrimientos en varios campos:
- Ciencia de polímeros: El diseño de sistemas de aglutinantes complejos (multi-componente) ha sido fundamental. Estos aglutinantes deben proporcionar fluidez durante la inyección, rigidez a la pieza en verde y ser fáciles de eliminar sin dejar residuos.
- Física de la sinterización: Un profundo entendimiento de los mecanismos de difusión atómica, crecimiento de grano y densificación durante la sinterización ha sido crucial para controlar la contracción, evitar la deformación y lograr las propiedades mecánicas deseadas en la pieza final.
- Producción de polvos metálicos: El desarrollo de métodos para producir polvos metálicos muy finos (típicamente por debajo de 20 micras), esféricos y con una alta pureza, como la atomización por gas o por agua, fue un requisito indispensable para el éxito del MIM. La morfología y el tamaño de las partículas son críticos para la fluidez del feedstock y la densidad final de la pieza.
Estado actual y futuro
Hoy en día, el MIM es una industria global en crecimiento. La tecnología MIM se utiliza para fabricar una enorme variedad de componentes complejos en sectores como:
- Automoción: Componentes de motores (balancines), sistemas de inyección de combustible, piezas de turbocompresores.
- Médico: Instrumental quirúrgico, implantes ortopédicos y dentales, componentes de endoscopios.
- Electrónica de Consumo: Conectores, disipadores de calor, carcasas de dispositivos móviles y relojes inteligentes.
- Armamento y Defensa: Componentes de armas de fuego (gatillos, martillos), sistemas de guiado.
- Aeroespacial: Pequeños componentes estructurales, piezas para sistemas de actuación.
El futuro del MIM se dirige hacia la producción de piezas aún más grandes y complejas, la expansión de la gama de aleaciones procesables (incluyendo aleaciones de alta entropía y vidrios metálicos amorfos), y una mayor integración con la industria 4.0 a través de la digitalización y la automatización completa del proceso.
¿Estás interesado en conocer todo lo que podemos hacer en Alfa MIMTech para tu proyecto de pieza MIM? Pincha AQUÍ y contacta con nosotros.