The manufacturing of metal parts has evolved significantly with the arrival of advanced technologies such as additive manufacturing and MIM (Metal Injection Moulding). These techniques allow for the creation of complex and precise components, opening new possibilities for industries like automotive, aerospace, and medicine. Although both methods can use metal powders as raw materials, each presents features, advantages, and disadvantages that make them more suitable for specific types of production. Let’s analyze the most important differences between these two manufacturing methods.
Common Characteristics of Additive Manufacturing and MIM
Both additive manufacturing and MIM share several characteristics that make them key technologies for creating complex metal parts:
- Materials: Both techniques use metal powders to form parts, either through injection into molds (MIM) or layer-by-layer addition (additive manufacturing).
- Geometric complexity: They enable the creation of shapes that are difficult or even impossible to achieve with traditional methods like machining or casting.
- Waste reduction: These are efficient processes in terms of material, using only what is necessary to create the final part.
- Advanced applications: Both technologies are widely used in industries where precision and efficiency are required, such as automotive, aerospace, medical, and electronics.
Additive Manufacturing: Features, Advantages, and Disadvantages
Additive manufacturing is based on a simple principle: building an object by adding material layer by layer. This makes it a revolutionary technique for prototyping and customized production.
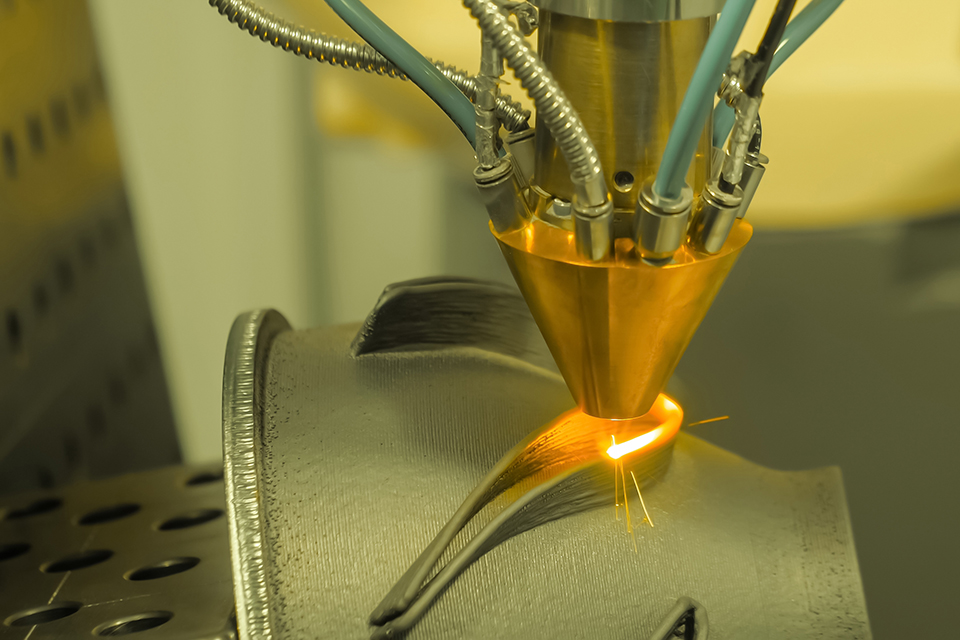
Additive Manufacturing
Advantages:
- Rapid prototyping and customization: The ability to manufacture customized parts without the need for specific tools is one of the strengths of additive manufacturing. It also allows for quick creation of prototypes to iterate on designs..
- On-demand production: It is perfect for producing unique parts or small series, reducing the need to maintain large inventories.
- Complex geometries: Most of these technologies allow the creation of complex internal shapes, such as integrated cooling channels or hidden cavities, which would not be possible with other manufacturing methods.
- Design flexibility: Design changes can be quickly implemented, speeding up the product development process.
Disadvantages:
- High costs: Although additive manufacturing is very efficient for customization, production costs are still high in most cases, especially in terms of equipment and specialized metallic materials.
- Production time: While it’s fast for prototypes, large-volume production can be slow compared to more traditional methods.
- Mechanical properties: Some parts produced with additive manufacturing exhibit anisotropy, meaning that mechanical properties can vary depending on the printing direction.
- Surface finish: Printed parts often require additional post-processing to meet surface quality requirements.
- Tolerances: Although there are differences among the various additive technologies, it can be said that they do not achieve the tolerances of traditional processes, requiring additional operations.
- Repeatability: As these technologies are not as mature as MIM, they still need to improve repeatability between batches and sometimes even within the same batch.
Metal Injection Moulding (MIM): Features, Advantages, and Disadvantages
MIM, on the other hand, is a process that combines the injection of a polymer with metal powder into a mold. After this molding process, the parts undergo a debinding and sintering phase to remove the binder and consolidate the metal. It is a particularly effective technique for mass production of small or medium-sized parts.
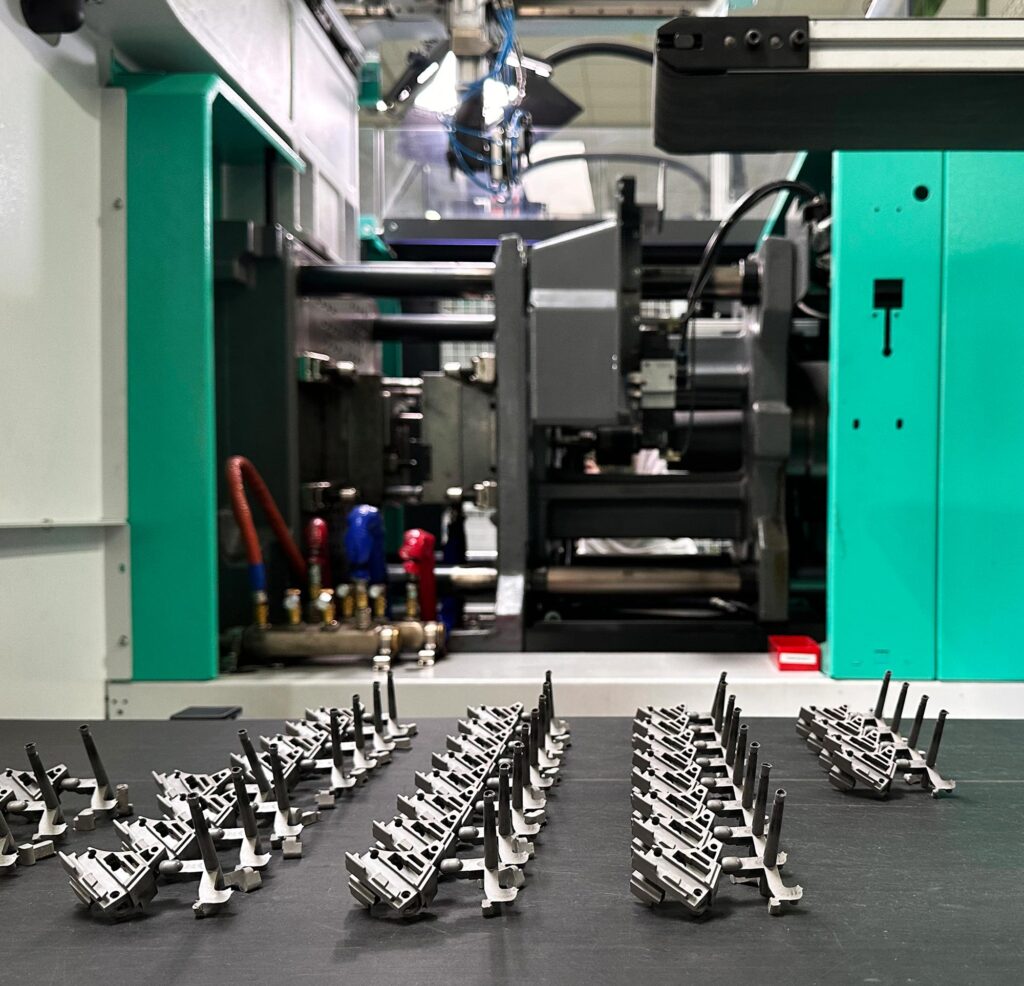
MIM
Advantages:
- Mass production: MIM is ideal for manufacturing large volumes of parts with relatively complex geometries and very tight tolerances.
- Lower production costs: Although the initial cost is high due to the need to create molds, MIM is highly cost-effective for large series production.
- Consistent mechanical properties: Parts produced by MIM have mechanical properties similar to those obtained by conventional methods like casting or forging.
- Material versatility: The process is compatible with a wide range of metals, including highly complex alloys such as titanium and superalloys.
Disadvantages:
- High initial costs: The need to create specific molds makes this process expensive for small productions, so it is more suitable for large series..
- Size limitations: MIM is more efficient for small to medium-sized parts; larger parts can present complications or be less cost-effective.
- Geometry limitations: While MIM allows for the creation of parts with complex shapes, it does not reach the level of design freedom offered by additive manufacturing, especially regarding internal geometries.
AM vs. MIM: When to Choose the Right Manufacturing Method
The choice between additive manufacturing and MIM depends largely on the specific needs of each project. Both methods have optimal applications depending on production requirements and part complexity.
Additive manufacturing: It is ideal for creating prototypes and unique or low-volume parts where customization and complex geometry are paramount. This method is widely used in the manufacturing of medical prosthetics, aerospace components, and parts with optimized internal structures.
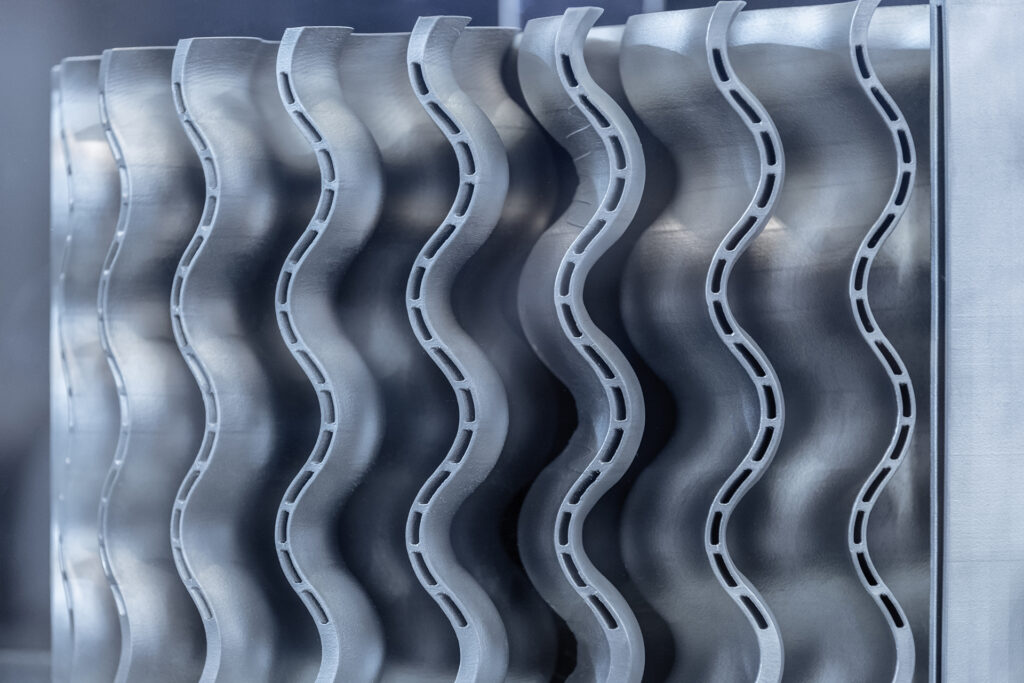
Part produced by laser sintering
MIM: It is better suited for mass production of small to medium-sized parts with moderately complex geometries, such as those found in the automotive industry, electronic devices, or watchmaking.
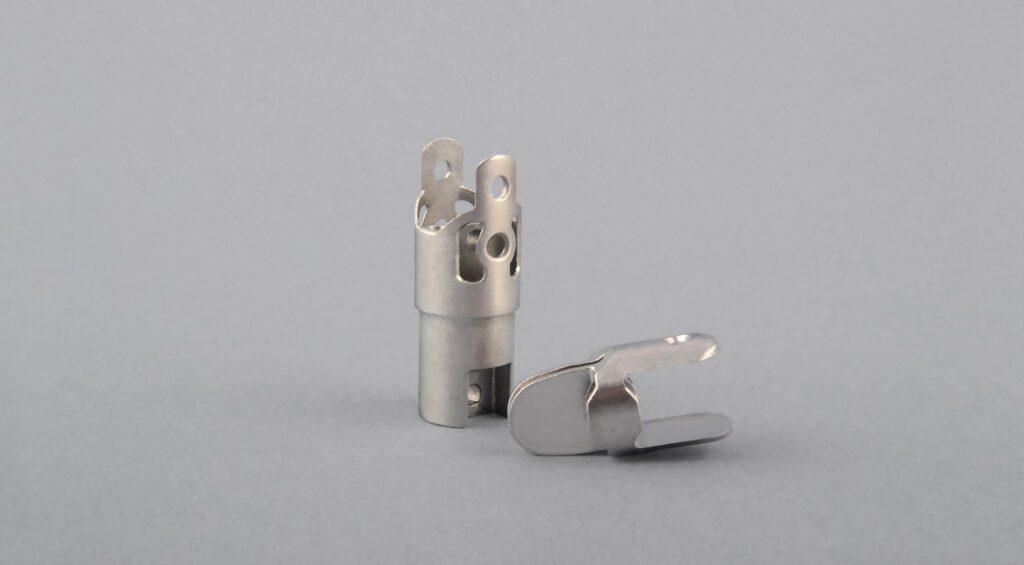
Part manufactured using MIM technology
In conclusion, additive manufacturing and MIM are complementary technologies in the production of metal parts. While the former excels in prototyping and complex geometries, MIM is a more efficient and cost-effective option for mass production of small and medium-sized parts with high precision. The choice between one or the other will depend on factors such as production volume, part size, and geometric complexity. Ultimately, both technologies are helping to revolutionize the metal manufacturing industry, each with its own strengths and challenges.