The development of Metal Injection Molding (MIM) technology is a fascinating story. This industrial process has revolutionized the manufacturing of complex, precision metal parts. Let’s take a detailed journey from its origins to its current state.
Background and origins of MIM technology: the fusion of two worlds
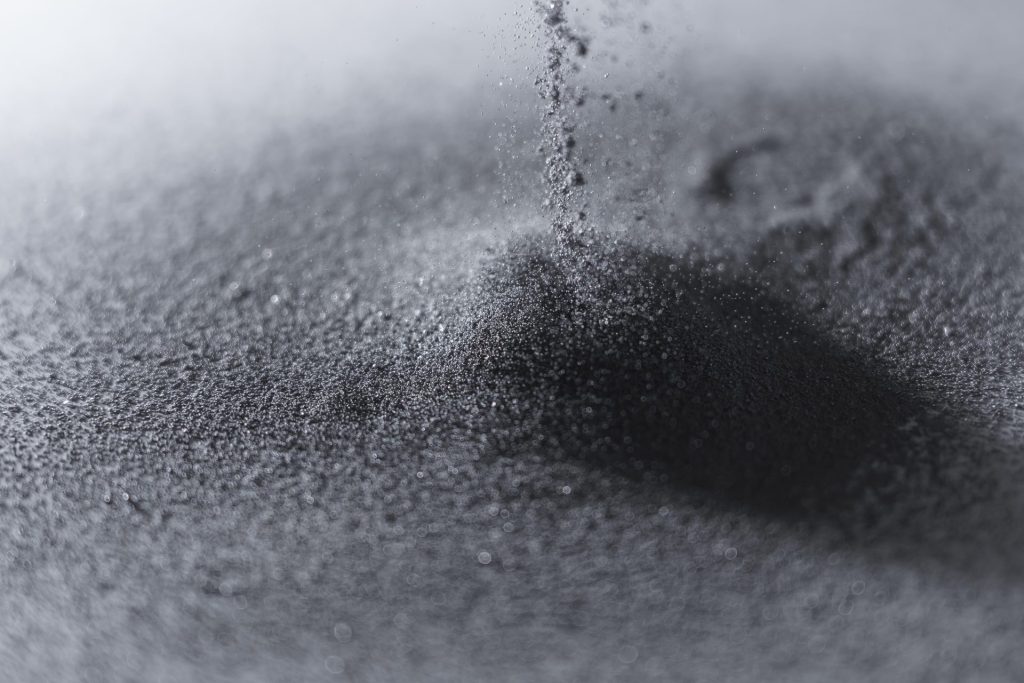
Base metal powder
MIM technology did not emerge from thin air; it was the result of the convergence of two well-established 20th-century manufacturing technologies: Powder Metallurgy and Plastic Injection Molding.
- Traditional Powder Metallurgy: This technique, with roots tracing back to antiquity (the Egyptians used it to make iron objects), involves compacting metal powder in a mold under high pressure to create a “green compact.” Subsequently, this part is heated in a high-temperature furnace (sintering) to fuse the metal particles, resulting in a solid, dense part. However, traditional powder metallurgy was limited in the geometric complexity of the parts it could produce. This process is also known as “press and sinter.”
- Plastic Injection Molding: Developed in the first half of the 20th century, this process allows for the mass production of plastic parts with very complex geometries It consists of injecting a molten polymer into a closed mold, where it cools and solidifies, taking on the desired shape.
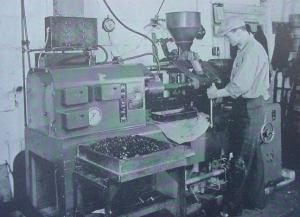
Plastic injection moulding machine in the 1930s
The seminal idea behind MIM was: What if we could inject metal powder into a mold with the same ease and design freedom as plastic?
The Pioneers and the birth of the concept (1920s – 1970s)
The earliest concepts resembling MIM date back to the 1920s, with attempts to mold ceramic powders However, the real push for MIM as we know it today began much later.
The theoretical origins of what would later lead to the development of MIM technology date back to the 1950s. In 1956, the Soviet scientist Petr Oskarovich Gribovsky published his study “Hot Casting of Ceramic Products,” where he established the conceptual and theoretical foundations for MIM.
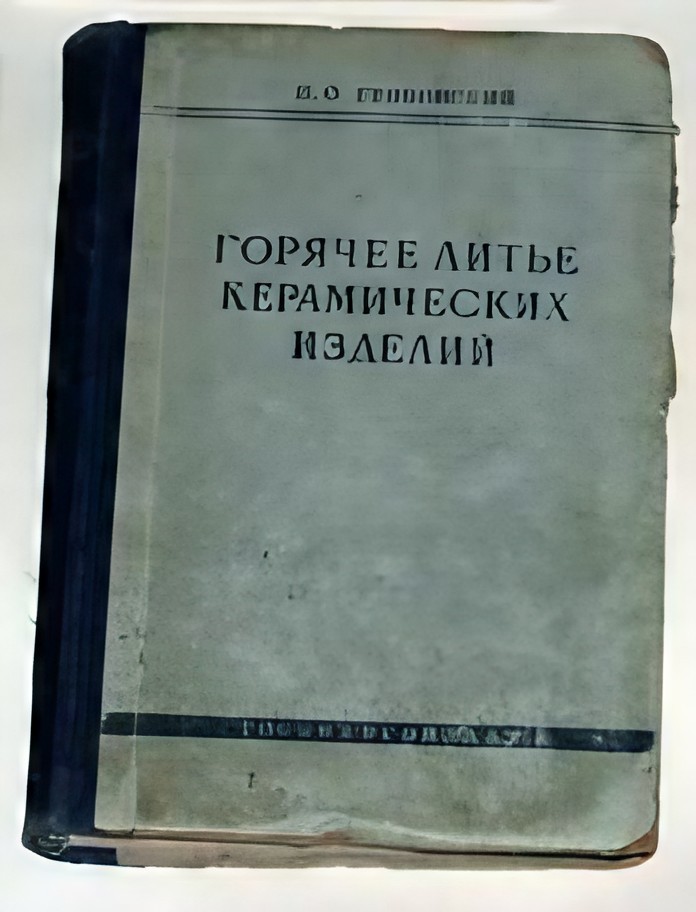
1965 edition of ‘Hot Casting of Ceramic Products’ by P. O. Gribovsky
His work described a “hot casting technology provides the ability to manufacture products from any solid material, from natural minerals, pure oxides, carbides, metals, etc., to multicomponent composite synthetic materials and their combinations,” although it was not applied to a specific industrial development to obtain such products.
We have to jump forward 20 years to find Dr. Raymond E. Wiech Jr. in the United States, a key figure in the MIM world, unanimously considered the “father of MIM.”
While working in California, he refined earlier concepts, adapting plastic injection molding for metals, and developed and patented the first commercially viable MIM process.
The MIM process: A technology full of challenges
Dr. Wiech and his team had the idea of mixing fine metal powders with a thermoplastic binder. This mixture, called “feedstock,” behaved like plastic at high temperatures, allowing it to be injected into a conventional plastic injection mold to form a “green” part.
This part was an exact replica of the mold cavity but was composed of metal particles held together by the binder.
The crucial challenge was to remove that binder without distorting the part and then sinter it to its final density. Wiech developed a two-stage process:
- Binder Removal (Debinding): The “green” part underwent a process to remove most of the binder. Initially, this was done through solvent debinding or slow thermal debinding.
- Sintering: The resulting part, now very porous and fragile (known as a “brown” part), was sintered in a controlled atmosphere furnace at temperatures close to the metal’s melting point. During this process, the metal particles fused, the part shrank predictably and uniformly, and it reached a high density (typically over 95% of the theoretical density).
Raymond Wiech’s work was decisive for the industrial adoption of MIM in the 1980s. His developments enabled:
- Establishment of reproducible and scalable processes: Wiech managed to standardize the formulation of metal powder and binder mixtures, as well as molding, debinding, and sintering methods, facilitating the mass production of complex parts with high precision and repeatability.
- Demonstration of commercial viability: Under his leadership at Parmatech, real components were successfully manufactured and marketed for demanding sectors such as automotive, electronics, and medical, which validated the technology in the industry and built confidence in its adoption.
- Intellectual property and technology dissemination: Wiech’s patents and the publication of technical results provided a secure and clear framework for other companies to invest in and develop the technology, accelerating its international expansion.
- Cost and complexity reduction: Thanks to Wiech’s advancements, MIM positioned itself as a cost-effective alternative to machining and other powder metallurgy processes, especially for parts with complex geometry and high production volumes.
In 1980, the first mass-produced MIM part, a rotor for a watch, won an award from the Metal Powder Industries Federation (MPIF), marking a milestone and introducing the technology to the world.
Technological Evolution (1980s – present)
Since Wiech’s pioneering work, MIM technology has undergone constant and significant evolution.
- 1980s: Expansion and new players:
- Following the initial success of the industrial application of the process designed by Dr. Wiech, new companies emerged that licensed the technology and began developing their own binder systems and processes.
- More complex alloys began to be processed, beyond basic steels, such as stainless steels and nickel alloys.
- 1990s: Advances in Binders and Sintering:
- One of the most important advances was the development of catalytic binder systems. This system, based on polyoxymethylene (POM), allowed for much faster binder removal (in hours, instead of days) by using nitric acid as a catalyst. This drastically reduced cycle times and costs, driving the massive adoption of MIM in Europe and Asia.
- Water-based debinding systems were introduced, offering a more environmentally friendly alternative to solvents.
- Improvements in sintering furnaces, with more precise control of atmosphere and temperature, made it possible to process reactive materials like titanium
- 2000s: Miniaturization and new materials:
- Micro-MIM was born, focusing on the production of millimeter or even sub-millimeter-sized parts with very tight tolerances. This opened doors to applications in medical devices, microelectronics, and high-end watchmaking.
- The portfolio of available materials expanded enormously, including:
- Refractory metals: Tungsten, Molybdenum.
- Titanium alloys: Crucial for medical and aerospace applications due to their biocompatibility and strength-to-weight ratio.
- Metal Matrix Composites (MMC): For example, tungsten carbide-cobalt for cutting tools.
- Precious metals: Gold, platinum.
- 2010s and Present: Simulation, Automation, and Additive Manufacturing:
- Process simulation: Advanced software allows for the simulation of mold filling, shrinkage during sintering, and prediction of potential defects, optimizing part and mold design before manufacturing.
- Automation: Robotics and real-time process control systems have increased the repeatability and efficiency of MIM production.
- Connection with Additive Manufacturing: Hybrid technologies have emerged that combine the design freedom of 3D printing with the mass production capability of MIM. For example, Binder Jetting technology shares many principles with MIM (use of powder and binder, followed by debinding and sintering) and is considered a complementary technology, along with other sinter-based additive technologies (FFF, LMM, etc.).
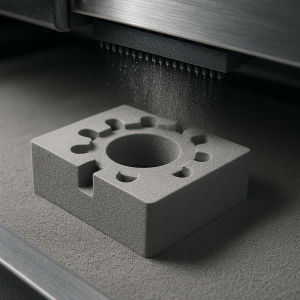
Binder jetting
Key scientific-sechnological discoveries
The evolution of MIM has been supported by discoveries in several fields:
- Polymer Science: The design of complex (multi-component) binder systems has been fundamental. These binders must provide fluidity during injection, rigidity to the green part, and be easy to remove without leaving residue.
- Physics of Sintering: a deep understanding of the mechanisms of atomic diffusion, grain growth, and densification during sintering has been crucial to control shrinkage, prevent deformation, and achieve the desired mechanical properties in the final part.
- Metal Powder production: The development of methods to produce very fine (typically below 20 microns), spherical, and high-purity metal powders, such as gas or water atomization, was an indispensable requirement for the success of MIM. . The morphology and size of the particles are critical for the feedstock’s fluidity and the final part’s density.
Current status and Future
Today, MIM is a growing global industry. The technology is used to manufacture a huge variety of complex components in sectors such as:
- Automotive: Engine components (rocker arms), fuel injection systems, turbocharger parts.
- Medical: Surgical instruments, orthopedic and dental implants, endoscope components.
- Consumer Electronics: Connectors, heat sinks, casings for mobile devices and smartwatches.
- Firearms and Defense: Firearm components (triggers, hammers), guidance systems.
- Aerospace: Small structural components, parts for actuation systems.
The future of MIM is headed towards the production of even larger and more complex parts, the expansion of the range of processable alloys (including high-entropy alloys and amorphous metallic glasses), and greater integration with Industry 4.0 through digitalization and full process automation.
Are you interested in knowing everything we at Alfa MIMTech can do for your MIM part project? Click HERE and contact us.